The Importance of Custom Plastic Molding Companies in Today’s Industrial Supply Chain
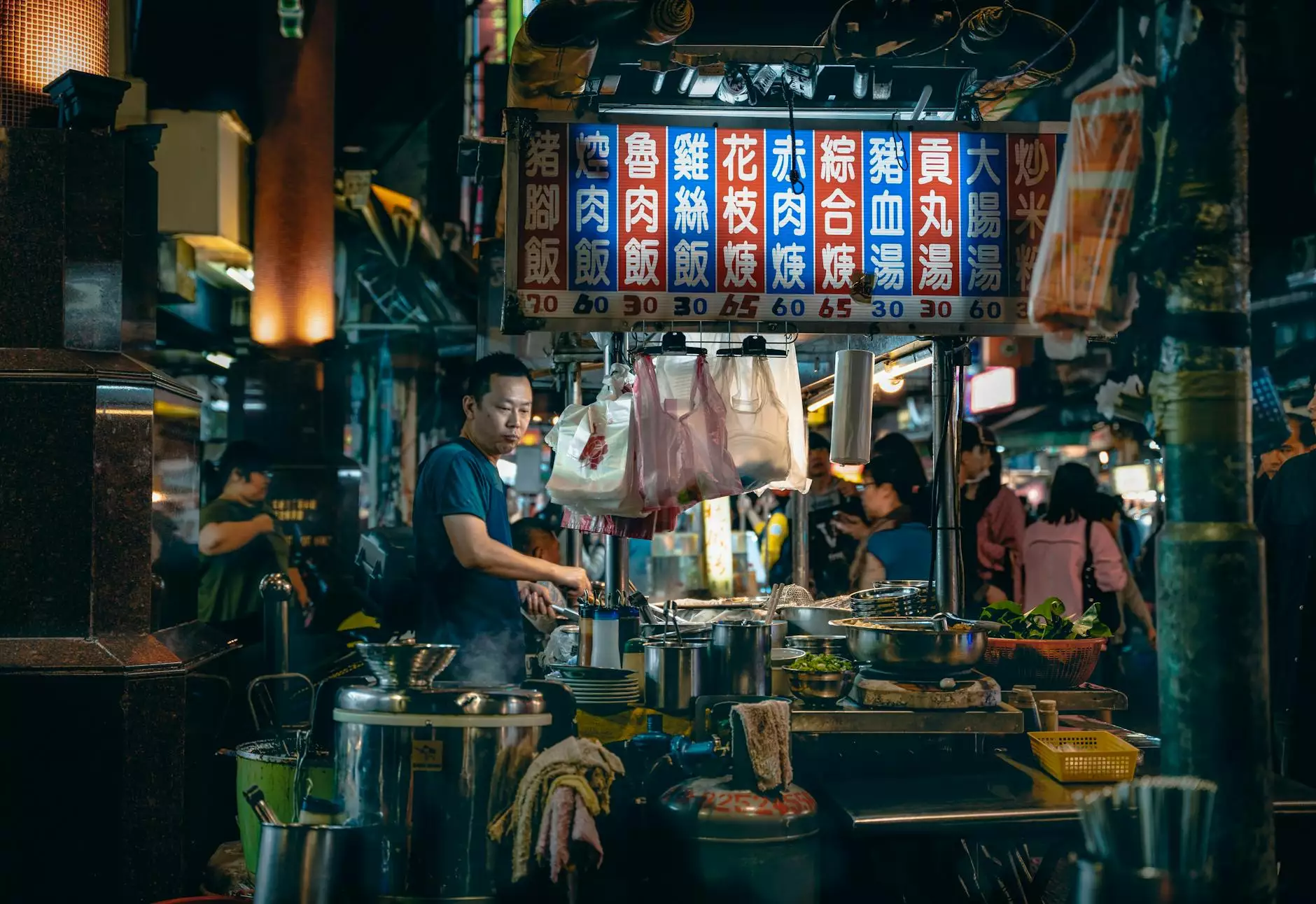
In the realm of modern manufacturing, the role of custom plastic molding companies cannot be overstated. As industries evolve, the demand for precision, efficiency, and customization continues to grow. Organizations from various sectors, including automotive, medical, consumer goods, and electronics, increasingly rely on these specialists to produce high-quality plastic components. This article delves into the significance of these companies, examining core services like machining, laser cutting, welding, plastic injection, and vulcanization, to illuminate their indispensable contribution to the industrial supply chain.
What is Custom Plastic Molding?
Custom plastic molding is a manufacturing process that creates plastic parts by molding raw plastic materials into specific shapes and sizes. It involves several techniques, each tailored to meet unique design specifications and production requirements. The most common methods include:
- Injection Molding: Ideal for mass production, this method involves injecting molten plastic into a mold.
- Blow Molding: Used for creating hollow plastic parts, such as bottles and containers.
- Rotational Molding: A process for producing large, hollow items by rotating a mold filled with plastic.
- Compression Molding: A traditional method wherein plastic is placed in an open mold and compressed into shape.
The finest custom plastic molding companies utilize advanced technology and expertise to ensure high precision and repeatability in production, making them pivotal for manufacturers looking to improve their product offerings.
Benefits of Partnering with Custom Plastic Molding Companies
Integrating custom plastic molding solutions into your production line offers multiple benefits:
1. Enhanced Design Freedom
One of the primary advantages of working with custom plastic molding companies is the design freedom they provide. Engineers and designers can innovate without constraints, as modern molding techniques accommodate complex geometries and intricate details. This flexibility enables companies to elevate their product designs, ensuring they stand out in a competitive market.
2. Cost-Effective Production
With economies of scale in mind, custom plastic molding lowers production costs in large quantities. The initial setup and tooling may require an investment, but as production scales up, the cost per unit decreases significantly. This makes it economically viable for companies to produce high-quality products.
3. Consistent Quality Control
Quality assurance is critical in manufacturing, and reputable custom plastic molding companies maintain strict quality control processes. Advanced technology, robotics, and inspection techniques are deployed to ensure every part meets stringent quality standards, thereby reducing waste and rework.
4. Versatile Material Options
Custom plastic molding enables the use of a wide array of materials, each tailored for specific applications. From durable thermoplastics to flexible elastomers, the versatility of materials available allows companies to select the best suited for their products, enhancing performance and longevity.
The Role of Supporting Services in Custom Plastic Molding
Beyond molding, companies like Sumiparts offer a range of additional services that complement plastic production:
1. Machining
Machining is a vital service that refines molded components to achieve precise tolerances, surface finishes, and functional features. This process can include:
- Milling: Removing material using rotary cutters for complex shapes and features.
- Turning: Producing symmetrical components by rotating the material against a cutting tool.
- Drilling: Creating holes in plastic parts for assembly or functionality.
2. Laser Cutting
Laser cutting technology allows for high precision cutting of plastic sheets and parts. This method provides clean edges and reduces material waste, making it highly efficient for intricate designs and quick prototyping.
3. Welding
In situations where parts need to be joined, welding becomes essential. Techniques such as ultrasonic welding and hot plate welding provide strong, durable joints while maintaining the integrity of the plastic components.
4. Vulcanization
For specific applications requiring enhanced durability and resilience, vulcanization is an integral secondary process. This method cross-links rubber molecules, improving heat resistance, elasticity, and overall performance in demanding environments.
Industries Benefiting from Custom Plastic Molding
The applications of custom plastic molding span various industries, each with unique requirements. Below are some key sectors leveraging this technology:
1. Automotive Industry
The automotive sector demands lightweight, durable components that can withstand varying conditions. Plastic parts play a crucial role in reducing weight, improving fuel efficiency, and enhancing design aesthetics.
2. Medical Field
In the medical industry, precision and sterility are paramount. Custom plastic molding companies produce pharmaceutical containers, surgical instruments, and diagnostic equipment while adhering to strict regulatory standards to ensure safety and efficacy.
3. Consumer Goods
From household items to electronics, consumer goods rely on custom molded plastics for functional and aesthetic components. The ability to create customized solutions helps brands differentiate their products in a crowded market.
4. Electronics
The electronics industry employs custom molding for housings, bezels, and interfaces, requiring high precision and reliability. With rapid advancements in technology, companies need to stay ahead by utilizing effective molding techniques to create innovative products.
Choosing the Right Custom Plastic Molding Company
When selecting a custom plastic molding company, it is crucial to consider several factors to ensure successful partnerships:
- Expertise and Experience: Look for companies with a proven track record in your industry.
- Technology and Equipment: Evaluate their capabilities concerning the latest molding technologies and machinery.
- Quality Certifications: Ensure that the company adheres to quality standards like ISO 9001 or relevant industry certifications.
- Customer Support: A responsive customer service team enhances collaboration and project success.
Conclusion: The Future of Custom Plastic Molding Companies
As we move into an era characterized by rapid technological advancements and increasing consumer demands, custom plastic molding companies will undoubtedly play a pivotal role in shaping the future of manufacturing. Their ability to provide innovative solutions, reduce costs, and ensure quality makes them invaluable partners in the production process. By integrating services such as machining, laser cutting, welding, and vulcanization, these companies help elevate product offerings across diverse industries.
In conclusion, engaging a reputable custom plastic molding partner not only boosts your manufacturing capabilities but also positions your business to thrive in a competitive landscape. Understanding your specific needs and collaborating with industry leaders like Sumiparts can propel your projects to new heights of success.